How Pulsed UV Light Decontaiminates
Pulsed UV light-based irradiation technology is the most attractive solution used to eradicate, and kill resistant microbes.
Overcoming biological resistance
The rising problem of biologicals becoming resistant to sanitizers and decontamination processes has led to an effort to find alternative approaches which kill resistant micro-organisms without harming the host cells. Pulsed UV light-based irradiation technology is the most attractive solution used to eradicate, and kill resistant microbes.
Among these wavelength ranges, UVC has the best potential ability to inactivate microorganisms because the wavelength of 250–270nm, is strongly and mainly absorbed by the nucleic acids of microbial cells and, therefore is the most lethal range of wavelengths.
The bactericidal mechanism of UVC is to cause damage to their RNA and DNA, which often leads to the formation of dimers between pyrimidine residues in the nucleic acid strands. The consequence of this modification is that the production of cyclobutane pyrimidine dimers (CPDs) causes deformation of the DNA molecule, which might cause defects in cell replication and lead to cell death afterwards.
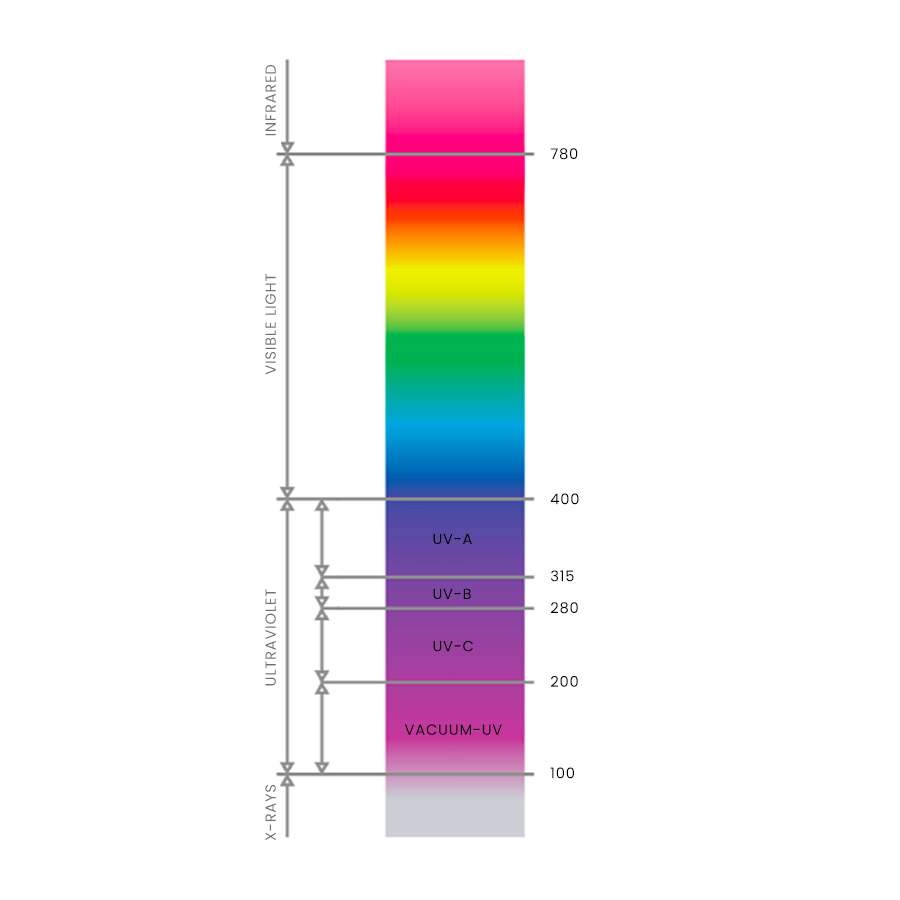
Electromagnetic Spectrum
Pulsed Light Technology
Pulsed Light Technology
How Pulsed UV Light is Used in Sterilization
Several pulses can be delivered per sec, creating sterilized material at a greater speed than conventional processes. The efficacy of the process has been tested against a broad range of microorganisms, including mold spores, bacteria (vegetative cells and spores), fungi, viruses, and protozoa.
The lamp unit consists of 1 or more inert gas lamps arranged to illuminate the desired treatment area. A high voltage cable connects the lamps to the power unit. To flash the lamp, a highvoltage, high-current pulse of electricity is applied. The high current passing through the gas in the lamp causes it to emit an intense pulse of light that lasts a few hundred microseconds.
The frequency of flashing is adjustable, allowing optimization of the process in conjunction with any particular processing speed. Systems are normally designed for each application to provide flexibility in the number of lamps, the flashing configuration, and the flash rate. Lamps can be flashed simultaneously or sequentially.
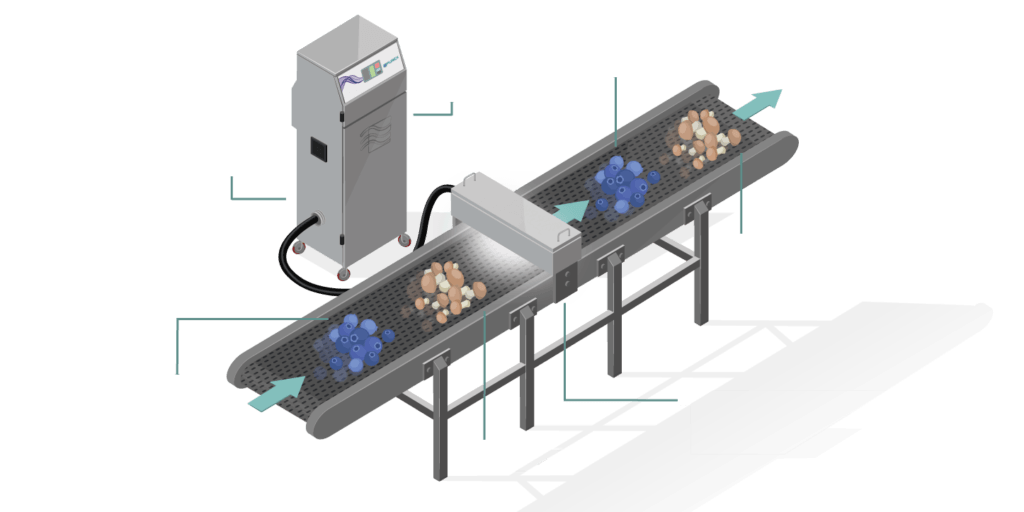
filter ozone gas created by Xenon UV light
Epoxy coated to prevent corrosion
Blueberries are disinfected without impacting taste or smell
Blueberries contaminated with pathogenic & spoilage microorganisms
Edible mushrooms
Pulsed UV light disinfects conveyor surface & sterilizes containers
Mushrooms enriched by UV light have Vitamin-D levels increased by up to 200%
How Pulsed UV Light is Used in Sterilization
Several pulses can be delivered per sec, creating sterilized material at a greater speed than conventional processes. The efficacy of the process has been tested against a broad range of microorganisms, including mold spores, bacteria (vegetative cells and spores), fungi, viruses, and protozoa.
The lamp unit consists of 1 or more inert gas lamps arranged to illuminate the desired treatment area. A high voltage cable connects the lamps to the power unit. To flash the lamp, a highvoltage, high-current pulse of electricity is applied. The high current passing through the gas in the lamp causes it to emit an intense pulse of light that lasts a few hundred microseconds.
The frequency of flashing is adjustable, allowing optimization of the process in conjunction with any particular processing speed. Systems are normally designed for each application to provide flexibility in the number of lamps, the flashing configuration, and the flash rate. Lamps can be flashed simultaneously or sequentially.
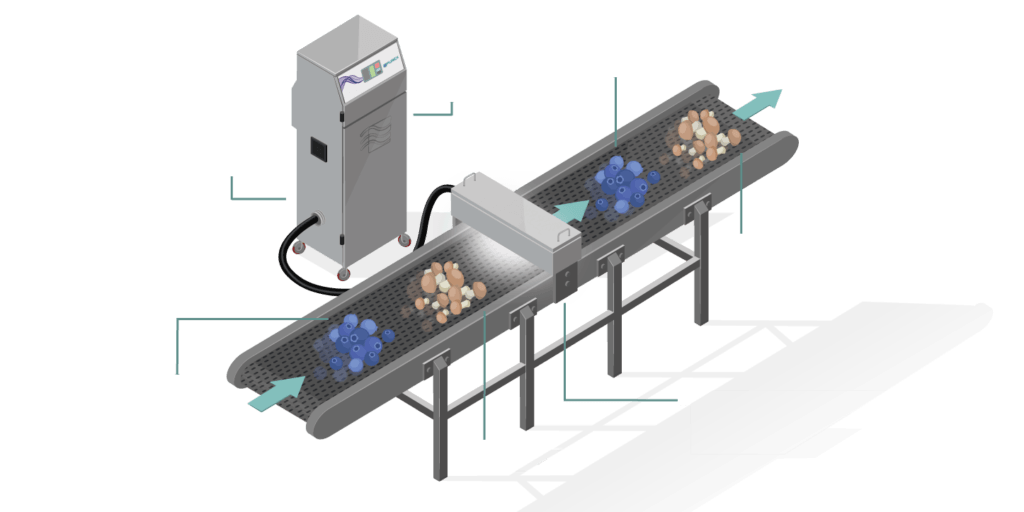
filter ozone gas created by Xenon UV light
Epoxy coated to prevent corrosion
Blueberries are disinfected without impacting taste or smell
Blueberries contaminated with pathogenic & spoilage microorganisms
Edible mushrooms
Pulsed UV light disinfects conveyor surface & sterilizes containers
Mushrooms enriched by UV light have Vitamin-D levels increased by up to 200%